Abstract:
The stainless steel wire mesh sleeve in the meta...
The stainless steel wire mesh sleeve in the metal hose joint is mainly to protect the bellows and withstand the medium pressure (mainly axial force) in the bellows. The net sleeve is wrapped on the outside of the bellows, and the two ends are welded with the bellows, end rings and joints.
(1) The screen sleeve is pulled off due to virtual welding
Because of the welding quality, the bellows, the ring and the steel wire mesh cover will cause some virtual welding (overburning or non-welding) of the steel wire during the three-in-one welding process. In this way, after the hose is installed in the pipeline, because of the uneven force on the steel wire, under the action of the medium pressure, the steel wire at the virtual weld will be pulled off first, so that the entire steel wire mesh sleeve will be pulled off, causing the outer drum of the bellows to fail and cause danger.
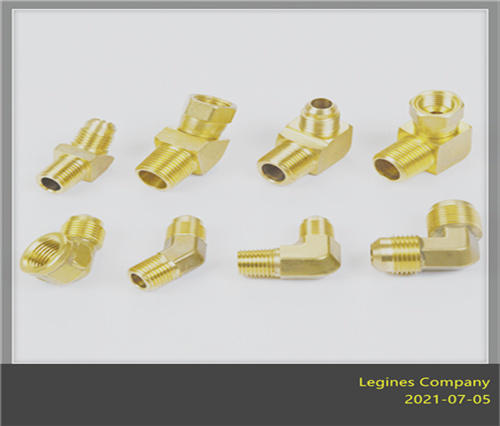
(2) Improper installation, causing the wire mesh to break
During the installation of the hose, due to improper installation or excessive pressure, the hose will be stretched and twisted. When the stress generated by stretching or twisting exceeds the ultimate strength of the hose steel wire mesh sleeve, the soft The net sleeve at the welded part of the pipe trinity or the net sleeve at other parts will be broken, and then the outer drum of the bellows will be stretched and damaged, causing medium leakage. For this reason, the design and selection should be correct, and the installation should be correct. In order to prevent this from happening, the welding quality should be improved. Before leaving the factory, the metal hose joints should be tested for water pressure and air tightness, and they can only leave the factory after passing the test.