Abstract:In the Stainless Steel Fittings system software, t...
In the
Stainless Steel Fittings system software, the elbow is to change the direction of the pipe. From an elbow perspective, it's 4590180. Depending on the project, other abnormal bends (eg 60°) may also be included. Stainless steel elbow welded product quality inspection method 1. Non-destructive testing, inspection of weld impurities, pores, cracks and other defects. At present, the commonly used detection methods are x-ray detection, ultrasonic detection and magnetic field detection. X-ray inspection is the use of X-ray photography to determine whether there are defects, how many and what type they are based on the film image. Then evaluate whether the weld is qualified according to the commodity technical standard.
The basic concept of ultrasonic inspection is to transmit ultrasonic inspection from the camera to the metal material. As ultrasonic waves travel to the page between the metal material and the gas, it is mapped out through the weld. If the weld is defective, the ultrasonic wave will be reflected to the camera and accepted, and the reflected wave will appear on the screen. By comparing and identifying the reflected wave and the ordinary wave, the size and location of the defect can be determined. Ultrasound inspection is much easier than x-ray inspection, so it is widely used. However, ultrasonic flaw detection can only be distinguished based on actual operating experience, which is inseparable from basic flaw detection. Magnetics can also be used to detect internal defects and small cracks on the weld surface.
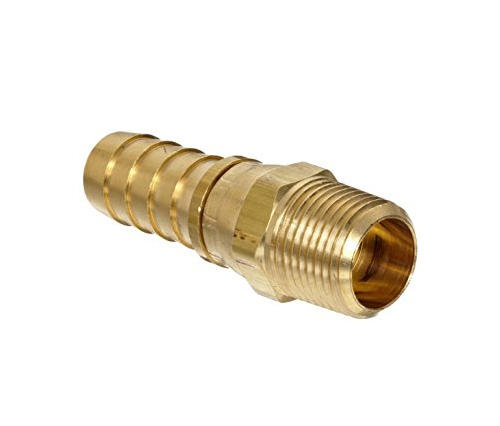
Visual inspection is generally observed with the human eye, sometimes with a height of 5-20 times. Through appearance inspection, it is found that there are defects such as joint errors, welding lumps, surface cracks, pores, slag inclusions, and welds on the surface of the welding seam of the stamping elbow. The appearance and size of welds can also be accurately measured using a butt weld detector or template. NDT can detect defects in welds, but cannot describe the physical properties of metal materials in thermally hazardous areas of welds. This experiment was performed on a test board. In order to ensure the same construction conditions, the test plates were welded to the vertical joints of the drum. Then test the physical properties of the board.
In concrete production and fabrication, there are only industrial trials of new steel butt welding. For high pressure vessels that must be sealed, a pressure test and/or standard pressure test must be carried out to check the tightness of the weld and its ability to withstand working pressure. By introducing water or steam pressure equal to 1.25-1.5 times the pressure (mainly gas) into the container, maintaining it for a period of time, and then observing the pressure drop and leakage in the container to judge whether the weld meets the standard.