Abstract:Reliability thread and compression of plumbing fit...
Reliability thread and compression of plumbing fittings
No matter where there is liquid, there is leakage-this is inevitable. Of course, leaks can cause monetary losses in terms of downtime and maintenance of industrial cleaning systems. Therefore, you ask what is the best anti-leakage measure.
Most leaks occur where one pipe is connected to another pipe. Valve piping, joints, pump and filter connections and tank fittings. Except for connections made by metal welding or brazing or polymer materials using metallurgical or adhesive methods such as adhesives, the liquid is only contained by two surfaces wedged into each other. Let us take a threaded joint as an example.
Threaded joints can be well used for certain extensible materials, such as iron, copper, aluminum, brass and polymers. When the fitting is tightened, the metal or polymer deforms to fill all the gaps to achieve a sealed connection. However, it is difficult to use threaded joints on hard materials such as stainless steel to ensure no leakage. The problem is that since the material is not easily deformed, there is almost always a small opening around the root of the thread. In many cases, attempts to stop the leakage by further tightening the fitting may result in greater leakage because the root of the thread will further separate as the metal deforms along its length. Teflon tapes and pipe "paints" are helpful, but they rarely provide reliable and permanent solutions. These materials may also be a source of pollution.

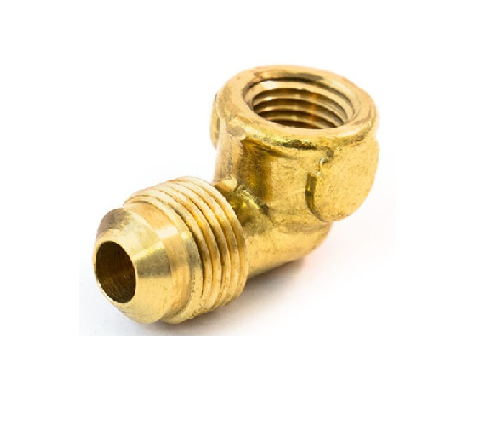
Alternatives to threaded joints include various compression joints, including compression joints with ferrules, which will compress around the circumference of the male tube when installed in mating female parts.
In a typical compression fitting, the ferrule (usually made of a softer material) is compressed to form a tight seal between the tube and the inner diameter of the fitting.
In a typical compression fitting, the ferrule (usually made of a softer material) is compressed to form a tight seal between the outer diameter of the tube and the inner diameter of the fitting.
Although threads are involved, their sole purpose is to provide the force required to compress the ferrule. The actual seal is separated from the thread.
The installation of the ferrule on the tube is an irreversible process, but if necessary, the joint can be disassembled and reassembled. In many cases, the leak can be repaired simply by tightening the nut more firmly. Compression fittings can be used in high-pressure applications, and as pressure increases (pressure tends to cause the tube to expand against the sleeve), it will become even more reliable.
Although compression fittings are generally considered more reliable than threaded fittings, there are still some potential problems. Generally, compression fittings are not as shock-resistant as welded or welded fittings. Repeated bending may cause the ferrule to lose grip on the tube. Also, for reliable sealing, the surfaces of the pipes to be connected must be reasonably rounded, and there should be no longitudinal scratches.
Compression fittings can be applied to materials from plastic to rubber to the hardest metal. It is important to choose the right accessories for the application. In softer materials, fittings may include inserts to support the inner diameter of the tube, thereby ensuring a good seal to its outer diameter. Other special modifications are also common to suit various applications of compression fittings.